Three Test Rigs for research and development for Pumps.
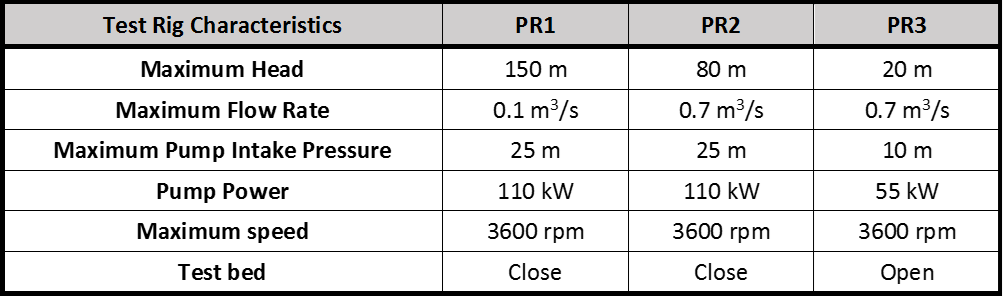
The role of the pump test is to verify the operating and performance data, to check functional reliability and to identify ways of improving and advancing products (research and development).
Within this context, static and dynamic pressures, flow rates, input and output powers, speeds, noise emissions, water temperature,the amount of air dissolved in water, strength levels, and vibrations are measured to assess the behavior of the pumps under standard and unconventional conditions.
Measuring instruments used
The measuring instruments used for acceptance tests must meet stringent precision requirements and must undergo official and in-house calibration (repeat calibration cycles recommended in DIN EN ISO 9906). These precision requirements are defined by the test class of the acceptance standard that is used.
Pressure measurements
-
In general, the following measurements are sufficient on a pump test facility: electronic pressure transmitters, pressure sensors and spring pressure gauges (class 0.25). Within this context, the standard maximum error level permitted for the instrument is 0.15 % of the full scale deflection.
-
In special cases, such as when recording processes (e.g. non-steady flow), suitable and/or miniaturized sensors and data loggers are installed for high-frequency recordings.
Measuring flow rates
-
On the pump test facility standardized throttles in accordance with ISO 5167 (Standard orifice plate, Standard nozzle and Standard Venturi nozzle) as well as instruments for measuring velocity MIF (magnetic-inductive flow metering) are installed.
Power measurements
-
For very precise measurements on the test facility, the torque meters between the motor and pump is installed. This is generally done in conjunction with speed measurement.
- If required, the electrical power consumed by the drive is measured using the two-wattmeter method.
Speed measurements
-
Speed measurements are taken on the pump test facility using digital counters which count discrete pulses with every revolution.
-
Usually 60 pulses per revolution are selected together with a count period of 1 second, it is possible increase the accuracy adopting 360 pulses per revolution.
Special measuring devices
-
Special requirements sometimes apply when taking noise and vibration measurements, NPSH measurements, and when carrying out model testing in water, rolling element and plain bearing tests, endurance tests and tests involving hot fluids handled.
-
In special cases, vibration, pressure pulsation measurements are taken using miniaturized sensor flush mounted.