Research activities
-
-
Extension of the hydraulic turbines operating range to provide electrical power system flexibility & stability for the integration of renewable.
-
Fundamental cavitation research and development of numerical tools.
-
Power Plant Dynamic Modelling and Live Cycle Assessment.
-
Development of Shrouded Wind Turbines with Wind-Lens Technology.
-
Development of Pump-Jet Adopted on Underwater Vehicle.
-
Projects
HydroCav CFD-Experimental Research
Cavity growth, development, and break-off during the periodic shedding process are studied for both steady and pitching 2D and 3D hydrofoils both numerically and experimentally.
Methods: Numerical Simulation, 3D Visualization, PIV, Experimental Analyses
Shrouded Wind Turbines with Wind-Lens Technology
The study is focused on the wind power enhancement technology named “Wind Lens”. The wind speed is increased by capturing and concentrating the wind energy locally.
Methods: Numerical Simulation, Experimental Analyses
PAT Pump as Turbine
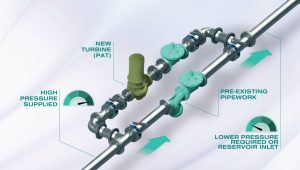
PAT-Pump-as-Turbine
Pumps as turbine are optimizes to create low-cost energy without environmental impact. PATs are the ideal solution in pipework where it is necessary to reduce the water pressure, or where the water flows by gravity into a tank, rivers or lakes, or even in mining or civil plants. Particularly where there are high energy costs, return on investment is very fast.
Methods: Numerical Simulation, Experimental Analyses
Effects of pump-surface-roughness on performance and cavitation
The effects of pump-surface-roughness on performance and cavitation will be evaluated by systematic experimental and numerical analyses. Turning, milling and painting processes will be considered and compared in terms of cost and benefit.
Methods: Numerical Simulation, Experimental Analyses
Multi-component Optimization of Inline Pumps
The aim of the research is a in-depth study, overlaying multiple perspectives and a multi-objective optimization of the inline pumps to obtain the optimum design able to increase the efficiencies at 0.5 Qd, 1.0 Qd and 1.5 Qd.
Methods: Heuristic Algoritms, Numerical Simulation, Experimental Analyses
Pump-Jet Propulsion
The study is focused on the optimization of Pump-Jet adopted on underwater vehicle.
Methods: Numerical Simulation, Experimental Analyses
Axial-Flow Pump as Turbine under Upstream Waves
The purpose of this study is to capture the morphology of vortices using the Omega vortex identification technique and investigate the relationship between upstream waves and the evolution of properties within the PAT system.
Methods: Numerical Simulation, Experimental Analyses
Optimization of Pumping Units
The project includes the mechanism of impeller inlet flow pattern on the pumping unit performance, the transient characteristics during variable speed and variable angle regulation, the pressure pulsation characteristics of the pumping unit performance .
Methods: Numerical Simulation
Pump Cavitation
Based on the visualization of the flow and identification of the cavitation morphology under different operating conditions, the evolution laws and three-dimensional structure of the cavitation flow field are defined on the basis of geometric and functional parameters.
Methods: Numerical Simulation
PAT Start&Stop Transition
The purpose of this study is to capture the morphology of vortices and unsteadyness using FFT, Wavelet and Omega vortex identification technique at part load, Shut-Down process and runaway transition in PAT (Pump as Turbine)
Methods: Numerical Simulation
Design optimization of pump-turbine to improve the stable working range in both the operating modes
Improvement in the Pump-Turbine Stability
Improvement in the Pump-Turbine Stability of S-Shaped Characteristics by Optimum design and using so-called misaligned guide vanes (MGVs) technique.
Methods: Numerical Simulation, 3D Visualization, PIV, Experimental Analyses
Life Cycle Assessment
The Life Cycle Assessment (LCA) is nowadays one of the most accredited assessment method for the quantification of damage along the whole life of the processes or activities and its outcomes can be correlated to the impacts on human health, on the quality of ecosystems and on the consumption of natural resources. By means of this approach, the TES group members study different processes, with a particular focus on those related to the energy conversion (for example, electric energy production from PV, wind turbines, or biomass; energy storage devices). The SimaPro software is used to perform LCA analysis (SimaPro is a registered trademark of PRé Consultants).
Photovoltaic Module Cooling Systems
Photovoltaic (PV) cells are sensitive to temperature variations due to changes in the ambient conditions: temperature, wind and solar irradiance intensity. Specifically, an increase of the PV cells operating temperature leads to an almost linear reduction of their performance. To overcome this issue, TES group members have developed a low-cost cooling system. The feasibility of the proposal has been numerically evaluated by means of a “in-house” mathematical model developed in Matlab Environment. Then, the real performance of the proposed system are evaluated experimentally investigated using the developed facility installed on TES Lab.
Power Plant Dynamic Modelling
In the current energy scenario, electricity is produced by a mix of fossil fuel power units and renewable energy power plants. After the deregulation of the energy markets and the large penetration of renewables, fossil fuel units need to be managed in a flexible way to compensate the power fluctuation related to the unpredictability of renewable energy plants like wind and solar. This means fossil fuel power plants able to start-up, shut down or change the load in a couple of minutes or even seconds. Obviously, strong load changes require, on the one hand, high ramp rates and, on the other hand, produce thermal and mechanical stresses which reduce devices’ lifespan. To detect the most stressed components and compute their life reduction, the most powerful instrument is the DYNAMIC ANALYSIS. In TES group, fossil fuel units and renewables power plants are modelled in OPEN MODELICA Language with the aim of testing start-up/shut down procedures and maximum tolerable ramp rates. Using simulation results, the life reduction of the most stressed component is computed using an “in house” procedure called “LifeTime Estimation Procedure” (LTE). Using the LTE procedure, it is possible to develop new and more reliable management strategies characterised by power plant components reduce lifetime reduction.
Design Optimisation, Part-load Behaviour and Dynamic Performance Prediction of Waste Heat Recovery Units
Waste Heat Recovery Units like Organic Rankine Cycles, Air Bottoming Cycles, Steam Rankine Cycles, etc. are powerful cycles able to increase the energy efficiency of industrial processes. In TES group, two “in-house” codes have been developed to design these types of units using Matlab Environment. Based on the Optimisation results, the most performing fluids and plant configurations are tested in ASPEN and DYMOLA Environments to predict part-load and dynamic performance. The best configuration is then analysed from an economic and an exergetic point of view.