Research activities
-
Cavitation modelling for steady and unsteady flow in pumps
-
Experimental andCFD comparison
-
Numerical optimization of impeller for very low NPSH
Projects
Cavitation in hydraulic machines is an important phenomenon to consider for performance prediction. Optimization of the impeller geometry requires a correct analysis of the occurrence of cavitation and an understanding of the flow structure and kinetic mechanism of cavitation instability and the effects on the flow field as the pressure level decreases.
Based on the visualization of the flow and identification of the cavitation morphology under different operating conditions, the evolution laws and three-dimensional structure of the cavitation flow field are defined on the basis of geometric and functional parameters.
The identification of the control factors influencing the diffusion and cavitation state will make it possible to define a method for optimizing the hydraulic model of key components such as the impeller and guide vane, and to promote the localization process of submersible pumps also for liquids other than water, such as LNG, and with different percentages of air in the liquid.
The results will be compared with the experimental data.
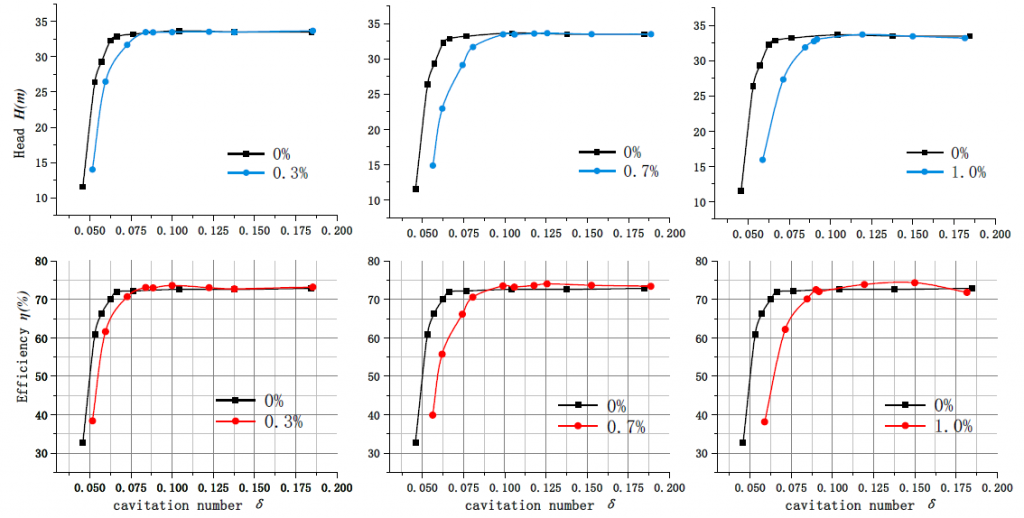
Tools
Facility – Pump Facility
Mesh Tools – ICEM
CFD Tools – ANSYS CFX
Post Processing Tools – Matlab and Python
Publications
Contacts
Prof. Giorgio Pavesi
Head of the TES Laboratories
+39-049-827-6768
Eng. Fanjie Deng